Detection Systems: The detection system comprises an intricate network of state-of-the-art sensors meticulously placed at crucial junctures within the assembly machine. These sensors are calibrated to detect even the slightest deviations in bottle movement and positioning. Utilizing cutting-edge technologies like machine vision and laser scanning, they continuously scan and analyze the flow of bottles, identifying potential issues such as misalignments, jams, or even irregularities in bottle shape or integrity. This granular level of detection ensures that no anomaly goes unnoticed, enabling swift intervention and resolution.
Automatic Shutdown: Upon detection of an anomaly, the assembly machine engages its automatic shutdown mechanism with split-second precision. This mechanism is engineered to instantly halt all machine operations, preventing any further progression of the issue. The shutdown sequence is meticulously designed to follow strict safety protocols, ensuring that all moving parts come to a complete stop and any potential hazards are neutralized.
Error Notification: In conjunction with the automatic shutdown, the assembly machine employs a multifaceted error notification system to communicate the detected issue to operators. This system utilizes a combination of visual, auditory, and digital cues to convey relevant information in real-time. Visual indicators such as flashing lights or illuminated displays immediately draw attention to the affected area, while audible alarms provide an additional layer of urgency. Simultaneously, detailed error messages or alerts are displayed on the machine's interface, providing operators with comprehensive insights into the nature and location of the issue.
Manual Intervention: In scenarios requiring manual intervention, operators are equipped with comprehensive training and resources to effectively address the issue at hand. Standard operating procedures outline clear protocols for safely accessing and troubleshooting the affected area of the assembly machine. Operators may utilize specialized tools, protective equipment, and ergonomic workstations to facilitate efficient resolution.
Recovery Procedures: To expedite recovery efforts and restore normal operation, the assembly machine is equipped with robust recovery procedures designed to autonomously resolve common issues encountered during production. These recovery procedures leverage the machine's advanced capabilities to execute precise corrective actions, such as reversing conveyor belts, adjusting gripper positions, or activating pneumatic mechanisms.
Adjustment Mechanisms: The assembly machine features a comprehensive array of adjustment mechanisms that empower operators to fine-tune and optimize performance for varying production requirements. Key components such as conveyors, guides, and sensors are designed with modularity and flexibility in mind, allowing for effortless customization and adaptation. Operators can easily adjust parameters such as speed, alignment, and pressure to accommodate different bottle sizes, shapes, and materials.
Diagnostic Tools: Advanced diagnostic tools are seamlessly integrated into the assembly machine's control interface, providing operators with unparalleled insights into its operational status and performance. These diagnostic tools leverage cutting-edge technologies such as machine learning algorithms and predictive analytics to analyze vast amounts of real-time data. Operators can access comprehensive diagnostic reports, trend analyses, and actionable recommendations directly from the machine's interface, empowering them to proactively identify and address potential issues before they escalate.
Bottle Automatic Assembly Machine
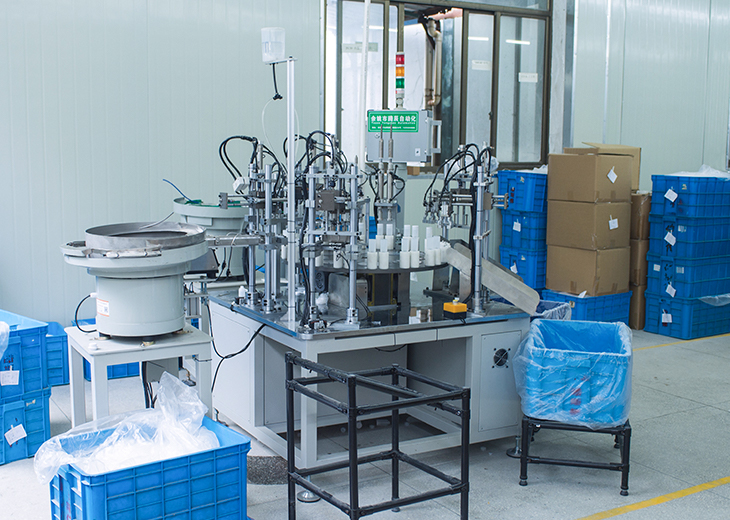