Lotion Pump Assembly Machine
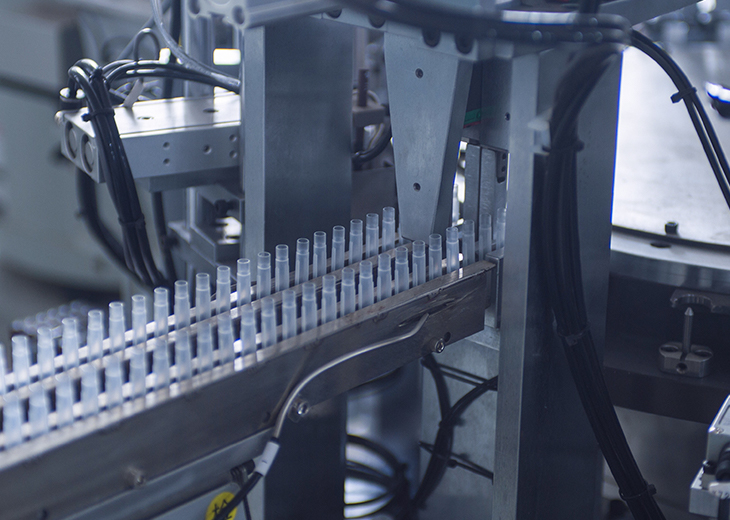
Trigger pump assembly machine TY-C1 7-piece assembly
Trigger pump assembly machine TY-C2 pump core 4 pieces
Trigger pump assembly machine TY-C3 pump core 5 pieces
Trigger pump assembly machine TY-C4 pump core testing
Trigger pump assembly machine TY-C5 piston collar assembly machine
Trigger pump assembly machine TY-C6 automatic nozzle machine
Trigger pump assembly machine TY-C7 duplex fog detection
Trigger pump assembly machine TY-C8 aluminum oxide head cap punching machine
Spray pump assembly machin TY-B1 all-plastic rosette gasket parts assembly (gun body, rosette, spring, piston, wrench)
Spray pump assembly machin TY-B2 all-plastic gun wrench 4 pieces (gun body, steel ball, spacer, bullet holder)