Adjustable Grippers or Fingers: These components are pivotal in accommodating the diverse shapes and sizes of items being packaged. They're often engineered with versatility in mind, featuring modular designs that allow for quick and precise adjustments to match the contours of each item. By utilizing materials with specific properties, such as varying levels of hardness or texture, these grippers can be fine-tuned to provide an optimal balance between grip strength and surface contact. Some advanced systems may incorporate pneumatic or hydraulic actuators, enabling dynamic adjustments during operation to adapt to changes in item dimensions or characteristics. This level of flexibility ensures that even the most delicate or irregularly shaped items can be securely handled without risk of damage.
Soft Touch Surfaces: Many modern packaging machines feature specially engineered surfaces on gripping components, designed to provide a gentle touch when handling fragile items. These surfaces often undergo meticulous material selection and surface treatment processes to achieve the desired properties. For instance, soft elastomers or polymers with high durometer ratings are commonly employed to minimize friction and distribute contact pressure evenly across the item's surface. Advanced surface texturing techniques, such as microstructuring or laser patterning, may be utilized to enhance grip stability while reducing the risk of surface abrasion.
Sensors and Vision Systems: Utilizing advanced technologies like proximity sensors, laser scanners, or machine vision systems, packaging machines can achieve unparalleled precision in item detection and orientation. These systems are integrated seamlessly into the packaging line, providing real-time feedback on the position, shape, and surface characteristics of each item as it moves through the assembly process. Machine learning algorithms and neural networks are often employed to analyze sensor data and make intelligent decisions regarding gripping strategies and handling techniques. The integration of 3D imaging technologies enables packaging machines to create detailed digital models of items, allowing for virtual simulation and optimization of handling procedures before physical implementation. By leveraging these cutting-edge technologies, packaging machines can ensure the reliable and accurate handling of even the most intricate or delicate items, minimizing the risk of damage and maximizing operational efficiency.
Flexible Packaging Techniques: To provide additional protection for fragile items, packaging machines often employ a variety of innovative packaging techniques and materials. For example, advanced inflatable packaging systems utilize air cushions or pillows to create a cushioning barrier around fragile items, minimizing the risk of impact damage during transit. Similarly, custom-designed foam inserts or molded pulp trays can be tailored to the precise dimensions of each item, providing a snug and secure fit within the packaging. The use of biodegradable and recyclable packaging materials aligns with sustainability initiatives while ensuring optimal protection for fragile items.
Variable Speed Control: Packaging machines are equipped with sophisticated speed control systems that enable precise adjustment of conveyor speeds, robotic arm movements, and other critical components. This granular control allows operators to optimize handling parameters based on the specific characteristics of the items being packaged. For fragile items, reducing conveyor speeds and implementing gradual acceleration and deceleration profiles can minimize the risk of sudden jolts or impacts that may cause damage. The integration of feedback control loops and predictive analytics enables packaging machines to dynamically adapt their speed and motion profiles in response to changing operational conditions or item characteristics.
Bag Package Automatic Assembly Machine
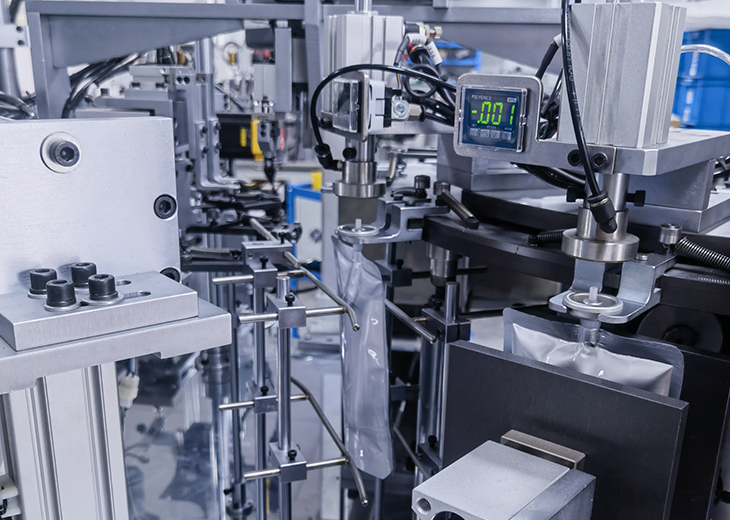