High Precision Handling: The trigger automatic assembly machine's robotic arms or gantry systems are not only precise but also employ a variety of gripping mechanisms tailored to the intricacies of trigger components. These mechanisms might include pneumatic grippers with adjustable pressure settings, vacuum suction cups with customizable suction levels, or even specialized magnetic clamps for ferrous components. By utilizing such advanced gripping technology, the machine ensures not only precise handling but also gentle manipulation of delicate components, minimizing the risk of damage or deformation during assembly.
Vision Systems: The machine's vision systems are not just basic cameras but incorporate cutting-edge technology such as high-speed image processors, multi-spectral imaging, and 3D depth sensing. These systems enable the machine to not only identify components but also to assess their quality, detect microscopic defects, and even perform real-time quality control checks such as surface finish analysis or dimensional measurements with sub-micron accuracy. By leveraging these advanced vision capabilities, the machine can confidently handle even the most intricate trigger designs, ensuring flawless assembly every time.
Customized Tooling: The machine's tooling solutions are not just off-the-shelf fixtures but are meticulously engineered using advanced CAD/CAM software and fabricated with high-precision machining techniques such as CNC milling or EDM wire cutting. These custom tooling solutions are designed not only to fit the unique geometries of each trigger component but also to optimize the assembly process for maximum efficiency and reliability. For instance, tooling might incorporate features such as quick-change mounting systems, self-aligning jigs, or even active heating/cooling elements to accommodate temperature-sensitive materials. By investing in bespoke tooling solutions, the machine ensures that even the most complex trigger designs can be assembled with ease and precision.
Flexible Programming: The machine's programming interface isn't just a simple graphical user interface but is a full-fledged software platform with support for advanced programming languages, scripting, and even machine learning algorithms. This allows operators not only to define complex assembly sequences but also to adaptively optimize those sequences based on real-time feedback from sensors and vision systems. For example, the machine might dynamically adjust assembly parameters such as torque, pressure, or speed based on the specific characteristics of each component, ensuring optimal performance without the need for manual intervention. By harnessing the power of advanced programming, the machine can handle even the most challenging trigger designs with unparalleled efficiency and precision.
Error Detection and Correction: The machine's error detection and correction mechanisms aren't just simple limit switches or basic error flags but are sophisticated systems incorporating redundancy, fault tolerance, and predictive analytics. For example, the machine might employ redundant sensors at key points along the assembly line to detect deviations from expected behavior and trigger automatic error recovery routines without interrupting production. The machine might utilize predictive analytics algorithms to anticipate potential failure modes and preemptively take corrective action before errors occur. By implementing such advanced error detection and correction mechanisms, the machine can ensure uninterrupted operation even in the face of unforeseen challenges, guaranteeing consistent quality and uptime for complex trigger assemblies.
Trigger Sprayers Assembly Machine
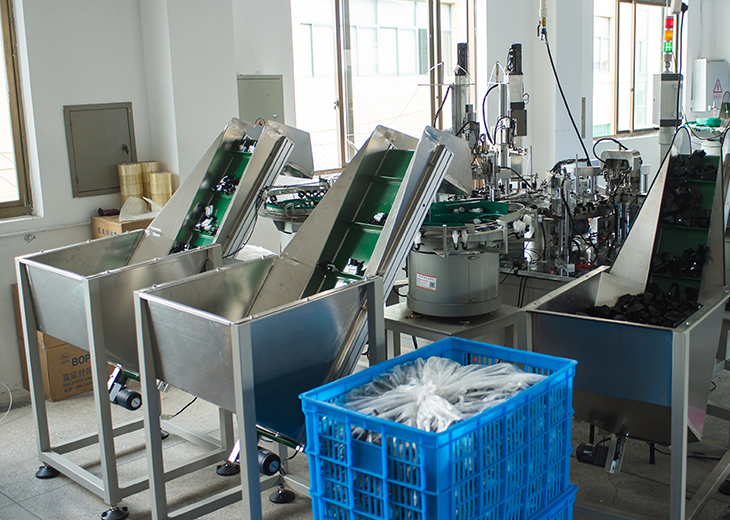