Feeding Mechanism: The feeding mechanism of the cap automatic assembly machine is a complex system designed to handle the intricate task of supplying cap components to the assembly line with utmost efficiency and reliability. Employing a combination of advanced technologies and precision engineering, this system ensures a continuous and uniform flow of components, minimizing any interruptions in the production process. Vibratory feeders, for instance, utilize controlled vibrations to convey components along a designated pathway, while gravity feeders rely on the force of gravity to move components downward along a sloped surface. Conveyor belts provide a versatile solution for transporting components over longer distances, offering customizable speed and configuration options to suit various production requirements. Each feeding method is carefully selected and optimized to maintain the delicate balance between speed, accuracy, and gentle handling of the components, thereby maximizing production throughput while minimizing the risk of damage or misalignment.
Orientation and Sorting: As cap components enter the assembly machine, they undergo a meticulous process of orientation and sorting to ensure that they are correctly aligned and positioned for assembly. This critical step is essential for maintaining the integrity and functionality of the assembled caps, as even minor deviations from the specified orientation can lead to defects or malfunctions in the final product. Optical sensors, for example, are employed to detect the precise orientation of components based on visual cues such as markings or patterns, while mechanical guides and pneumatic actuators provide physical manipulation to align components in the desired orientation. Through sophisticated feedback mechanisms and real-time adjustments, the assembly machine continuously monitors and corrects any deviations from the prescribed orientation criteria, ensuring consistent and reliable performance throughout the assembly process.
Reject Mechanism: To uphold the highest standards of quality and precision, the assembly machine is equipped with a robust reject mechanism that is capable of swiftly identifying and removing any defective or improperly oriented components from the assembly line. This proactive approach helps to minimize the risk of producing substandard caps and ensures that only components meeting the stringent quality criteria proceed further in the assembly process. Upon detection of a deviation from the specified quality standards, such as defects in shape, size, or orientation, the reject mechanism initiates immediate corrective action to remove the faulty component from the production line. This may involve diverting the component to a designated reject bin or chute, halting the assembly process temporarily to address the issue, or triggering an alarm to alert operators to the problem.
Integration with Assembly Stations: Once the cap components have been successfully fed, sorted, and quality-checked, they are seamlessly integrated into the assembly stations where the final assembly takes place. This integration process is facilitated by a sophisticated array of automated mechanisms and precision-engineered equipment, each carefully synchronized to ensure smooth and efficient operation. Rotary indexing tables, for example, provide a versatile platform for positioning and transporting components between different assembly stations, rotating at precise intervals to align components with the required tools and fixtures. Pick-and-place robots offer a flexible solution for handling components with varying shapes, sizes, and orientations, utilizing advanced vision systems and robotic control algorithms to grasp and manipulate components with precision and dexterity.
cap automatic assembly machine
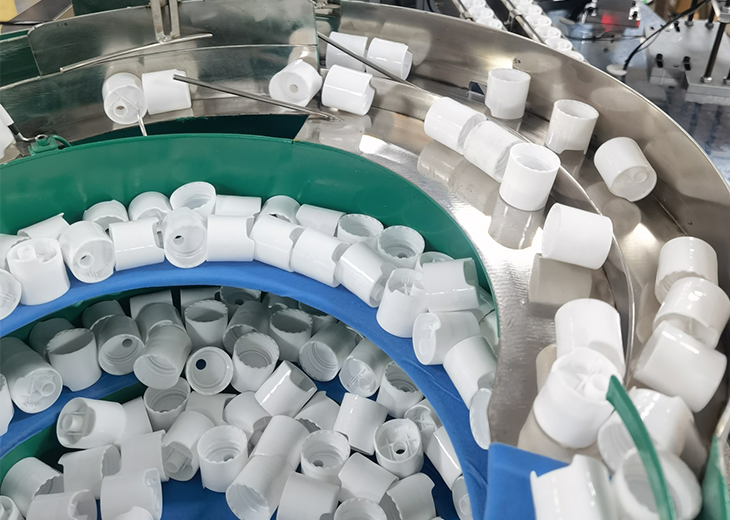