Vision Systems: These systems are comprised of advanced cameras strategically placed along the assembly line. These cameras possess high-resolution capabilities and are equipped with lenses optimized for capturing detailed images of components. The captured images are then processed using cutting-edge image recognition algorithms, capable of discerning even the minutest defects or deviations from expected standards. Through sophisticated software, these systems compare the captured images against a comprehensive library of reference images representing ideal components. Any disparities or irregularities detected trigger immediate alerts or corrective actions, ensuring that only flawless components proceed through the assembly process.
Sensor Integration: The automatic assembly machine incorporates a myriad of sensors meticulously integrated into every facet of the assembly process. Proximity sensors are employed to detect the presence or absence of components at designated stations, ensuring that each step in the assembly sequence occurs only when all requisite parts are properly positioned. Force sensors are strategically placed to measure the pressure exerted during crucial assembly tasks, ensuring optimal seating, alignment, and engagement of components. Laser sensors are deployed to meticulously scan component surfaces, meticulously checking for imperfections, blemishes, or irregularities that could compromise product quality. Through seamless integration and precise calibration, these sensors provide real-time feedback, allowing the system to swiftly identify and address any anomalies or deviations from prescribed standards.
Tolerance Checks: Prior to and during the assembly process, the automatic assembly machine meticulously conducts tolerance checks to ensure that each component meets the stringent dimensional requirements specified for the final product. Utilizing state-of-the-art measurement tools and precision instrumentation, the system meticulously verifies that each component falls within the prescribed tolerances for critical dimensions such as length, width, thickness, and geometry. Through meticulous calibration and validation procedures, the machine ensures that its measurement capabilities remain accurate and consistent over time. Any components found to deviate from the specified tolerances are promptly flagged for further inspection or rejection, ensuring that only components of the highest quality are utilized in the assembly process.
Torque Control: To guarantee the structural integrity and reliability of assembled products, the automatic assembly machine employs advanced torque control mechanisms to precisely regulate the tightening of fasteners and connections. Torque sensors, integrated into assembly tools or fixtures, meticulously measure the rotational force applied during fastening operations. These sensors provide real-time feedback to the control system, ensuring that fasteners are tightened to the precise specifications required for optimal performance. Through meticulous calibration and validation procedures, the machine ensures that torque levels remain within the prescribed range, preventing issues such as under-tightening, over-tightening, or damage to components. By maintaining strict control over torque levels, the machine guarantees that assembled products meet or exceed the most demanding quality standards.
Aerosol Valve Assembly Machine Factory
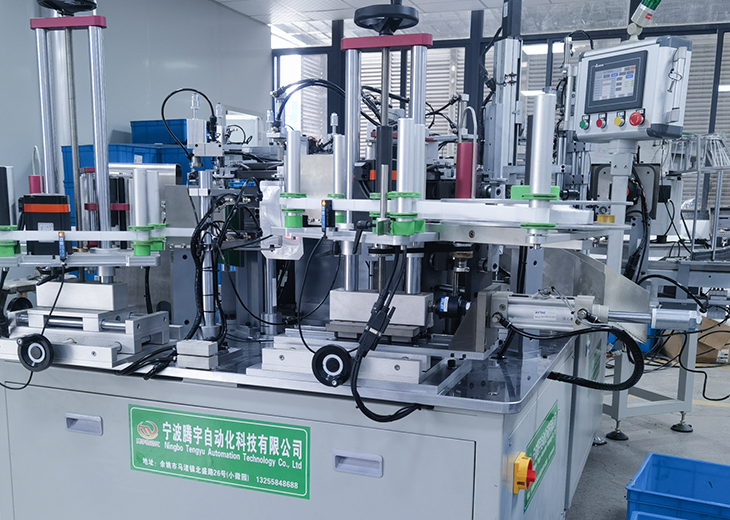
The aerosol valve is composed of three parts: cap, nozzle and stem. The machine is fast, efficient and low cost to assemble. The machine is capable of automating the assembly of the three parts. The machine is controlled by advanced high performance PLC with touch screen, and adopts variable frequency speed regulation to adjust the production schedule according to your production needs. Easy operation reduces the requirement for workers.